Looking Across Borders for a Fresh Perspective on Asphalt Production
Looking Across Borders for a Fresh Perspective on Asphalt Production
It's the ultimate success story: The perfect technical solution meets the ideal business plan.
We are often focused on experiences in our own country and don’t always take a close look at what happens in other locations, in this case Madrid. We tell ourselves, “But the market is different abroad. It would never work at home.”
Perhaps. Yet beyond our borders, roads are still built with filler aggregates and bitumen, just as they are at home. (On some occasions, they might be built even better.) The mix is produced by the same asphalt-mixing plants, unless they are adapted to some local preference. Even these differences are often more philosophical than technical. (For instance, some countries use a continuous plant instead of a batch plant.)
All asphalt producers, or at least those in Western Europe, have similar needs. Among them is maximising the use of recycled asphalt (RAP) in a way that least impacts the environment. That entails recovering as much of the old binder as possible, and even more crucial, minimising emissions. Sound and odour reductions are also important.
What distinguishes businesses between neighbouring countries is often the organisational structure. France is the master in this area, with three large companies controlling (in one fashion or another) more than 80% of asphalt production.
Such ownership structures mean that more and more plants are managed by several companies or entrepreneurs – perhaps through a temporary consortium for a large project or as part of an ongoing agreement.
These partnerships often result in a single larger plant replacing many smaller production facilities in the same territory. The larger plant is invariably more modern and technologically advanced than those it replaces.
The advantages of this approach are significant.
Higher production brings with it a host of benefits, including a reduction in the cost of raw materials given the high volume being acquired.
The plants’ efficiency also reduces material waste, another key cost-saver.
Fixed costs related to plant purchase, maintenance and personnel are spread across several owners.
Maintenance and parts replacement tend to be completed in a timelier fashion with a single larger plant than multiple smaller facilities.
These advantages create two significant outcomes:
There is a reduction in the cost per tonne of production.
The reduction in the number of plants in the territory has a positive environmental impact, with emissions from a single larger plant dramatically lower than the combined emissions of the plants it replaces.
There are many winners, including a community that benefits from a single operation as fewer residents live near a plant.
The example of Madrid
This is the context in which the project in Madrid was born. Local asphalt producers joined forces with the larger International Construction Group.
Spain’s capital city has more than 3 million inhabitants, not including surrounding areas. A vast road network within the city limits stretches for hundreds of kilometres. Tunnels are often utilised to minimise the impact in the urban location.
Demand for asphalt mix is strong given the expansive roadway system. Yet equally important is the need to reduce the number of plants, including some in previously isolated locations where residents have since expanded. Plants now need to be placed in more strategic locations. The days of a plant that produces 70,000 tonnes per year being situated in an urban location is no longer the best solution.
The plant of choice for the consortium led by a large French-Spanish construction company in Madrid was the Ammann ABP 320 Universal Asphalt-Mixing Plant. It has several winning features that resulted in its selection.
The flexible plant is capable of being expanded in the future to easily adopt changes and new requirements. (Specifically, it can accommodate the potential addition of the RAH100 dryer, which is exclusively used for heating RAP.)
Immediately available to the consortium is the second-generation RAH50, with a recycling ring on the dryer cylinder. The RAH50 enables the use of up to 50% RAP and substantially reduces emissions.
Up to 40% cold RAP can be introduced through the metering system. Two hoppers can be housed at the top of the plant. Independent weighing and metering belts can handle both hot and cold mixes.
A wide range of technical mixes can be produced through the introduction of foamed bitumen, pigments and multiple additives.
The Ammann ABP 320 Universal plant is equipped with a hot stock under screen, where 200 tonnes of hot aggregates are separated by grain sizes and aggregate type (limestone and basalt, for example). The materials can be stored for many hours, thanks to extremely thick 200-mm insulation.
A finished product silo has a capacity of more than 400 tonnes of mix and can feed two separate truck-loading lines. Mix temperatures can be maintained for many hours because the silo is also outfitted with 200 mm of insulation, more than double the highest standard on the market.
In addition, the Ammann as1 Control System adds efficiency. It integrates all components and reduces waste. The system has proven itself at hundreds of locations around the world, and it is appreciated for its advanced technology, intuitive operation and safety. It monitors processes and can add further functions in the future.
Insight into the RAH50
In an industry where empirical evidence and conversations at the jobsite have driven product development, advanced data and simulation are now propelling that process. While there is a place for these approaches, they are best utilised in conjunction with the more advanced tools now available.
The end result is a new dryer cylinder mechanically capable of handling up to 50% recyclables. It offers a 30% higher energy efficiency index compared to a traditional cylinder. This is confirmed by the fact that the temperature of the fumes exiting the cylinder is more than 30° C lower than any other cylinder, demonstrating that all energy is exchanged with the aggregates.
The use of proprietary steels allows the RAH50 to meet performance expectations while maintaining unrivalled durability. Emissions are extremely low due to the perfect dryer-burner cylinder combination (also designed and built by Ammann) and the patented system of introducing RAP. The process involves gently and gradually heating RAP to prevent damage to the bitumen. The slow, progressive heating of the RAH50 contrasts with the more “violent” method utilised by other products. It is no coincidence that hundreds of RAH50 units have been sold worldwide in the last 10 years.
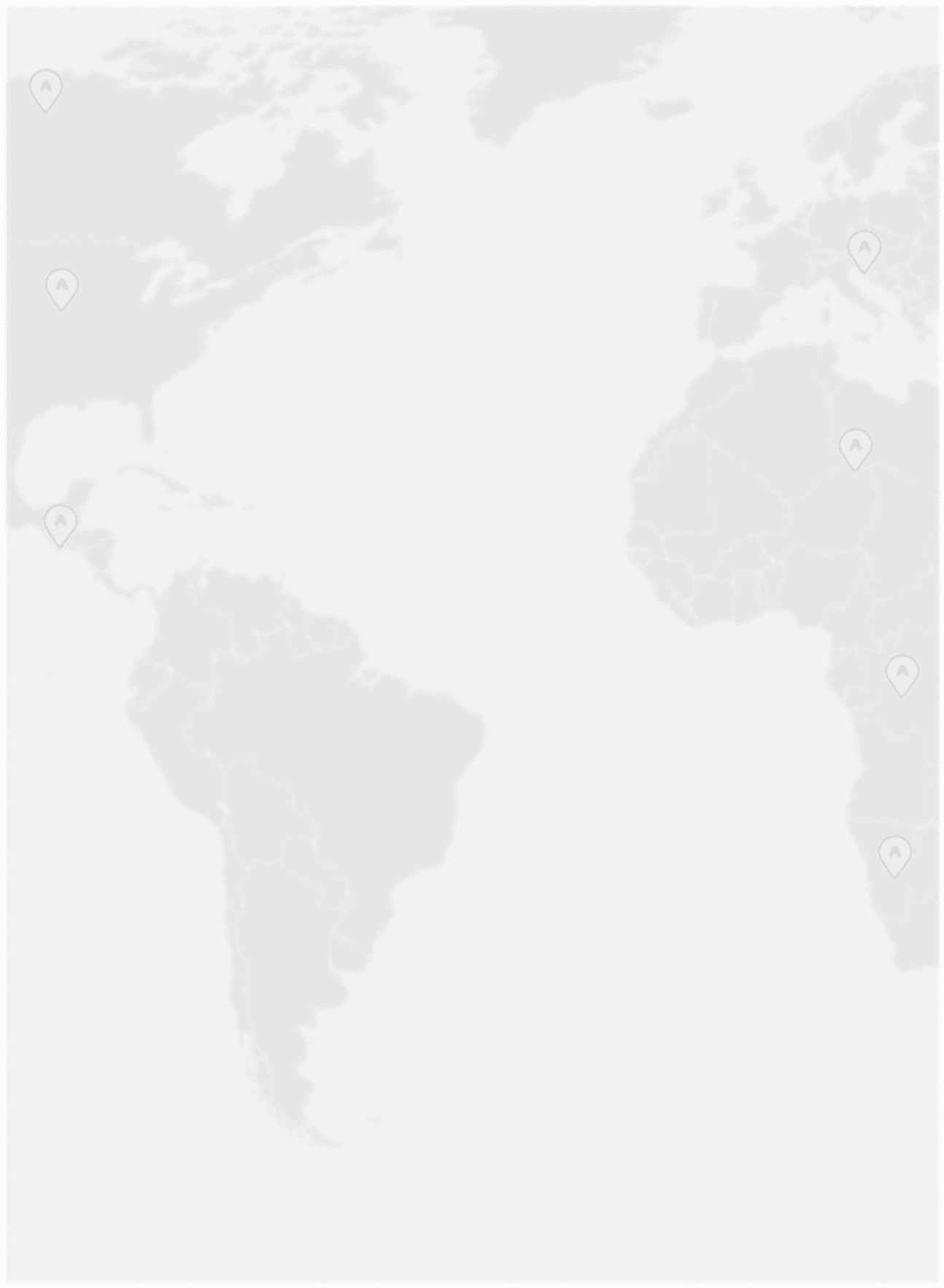
Contact Form
Schedule online meeting
Get in touch with us to meet a sales representative near you
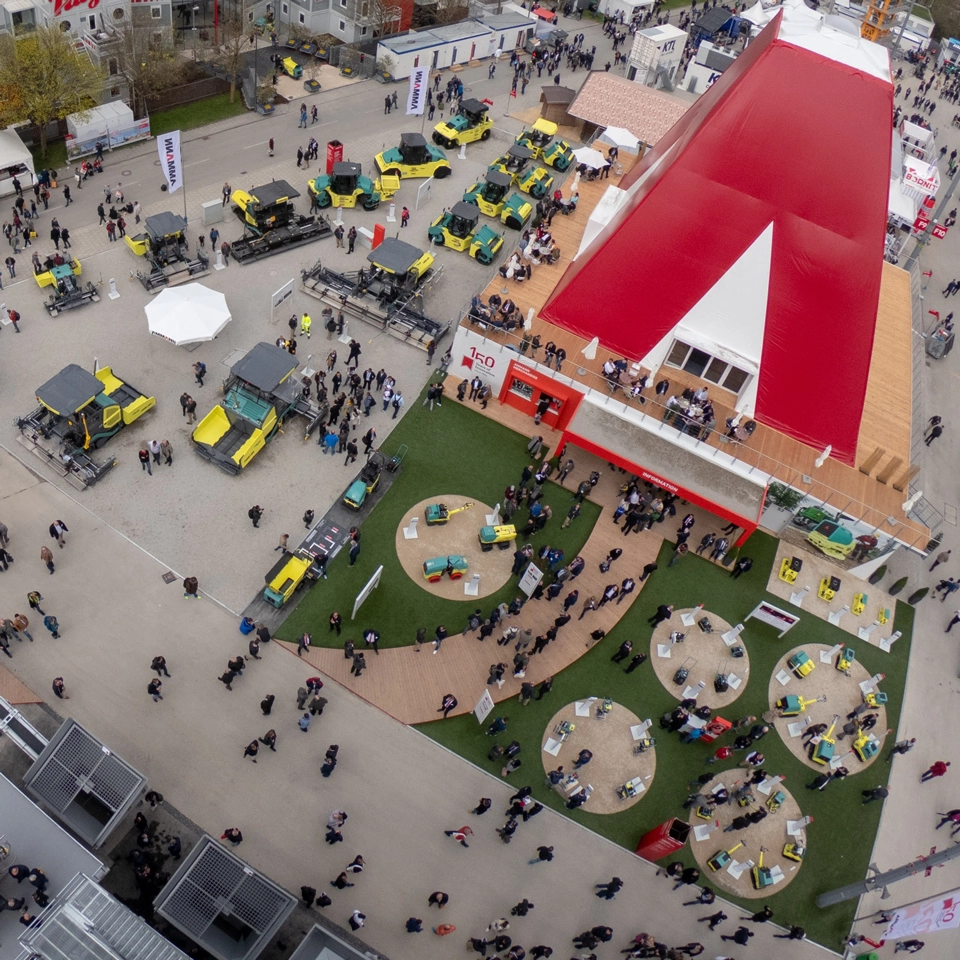